Surface Atmospheric-Pressure Plasma Printing (SurfAP3®) is a plasma printing technology developed at the Leibniz Institute for Plasma Science and Technology, in Greifswald, Germany.
- Our plasma printing technology is maskless, therefore no mask or shaped electrodes are needed to produce the desired patterned surface modification. Therefore, direct writing for surface modification and microfabrication is possible using atmospheric-pressure plasma, and moreover, no vacuum equipment is needed.
- The novel INP-developed, patent pending plasma source microPulsar allows true submillimeter and micrometer resolution, offering a linewidth resolution at least 10x finer than the currently offered resolution in the market for maskless plasma thin film depositions, as seen in Figure 1, as our minimum linewidth resolution starts from 50 μm. This also means that fine cleaning and activation is also possible at micrometric scale.
- Unlike other plasma sources, ours can precisely modify electrically and non-electrically conductive materials, which is a significant advantage considering that polymers and glass are the preferred choice for the fabrication of biochips.
- Our highly efficient plasma source is compact and has low input power (< 5 W) and gas flow consumption (< 300 sccm), therefore the operational cost are extremely low, and the equipment can be easily mounted in high-throughput setups (e.g. production lines) and/or OEM equipment. Integrated multiple plasma devices possible for scalability.
- Our method avoids damage to the precursors used for chemical functionality and/or cross-contamination of the plasma source depending on the precursor injection method selected. Moreover, it is possible to add nanoparticles to create new functionalities.
- Our plasma nozzles are easily exchangeable.
- Our innovative chemical precursors and gases used are based on green chemistry, avoiding harmful substances. Furthermore, the plasma does not produce toxic byproducts.
- Our specialized knowledge of maskless plasma printing allow us to develop and offer add-ons to increase productivity, recipe optimization, monitoring, traceability and quality assurance. For example, the plasma source and process can be monitored in real-time, and we are currently developing a Smart Machine Vision module based on machine-learning capabilities to inspect and assess the quality of the plasma printed patterns.
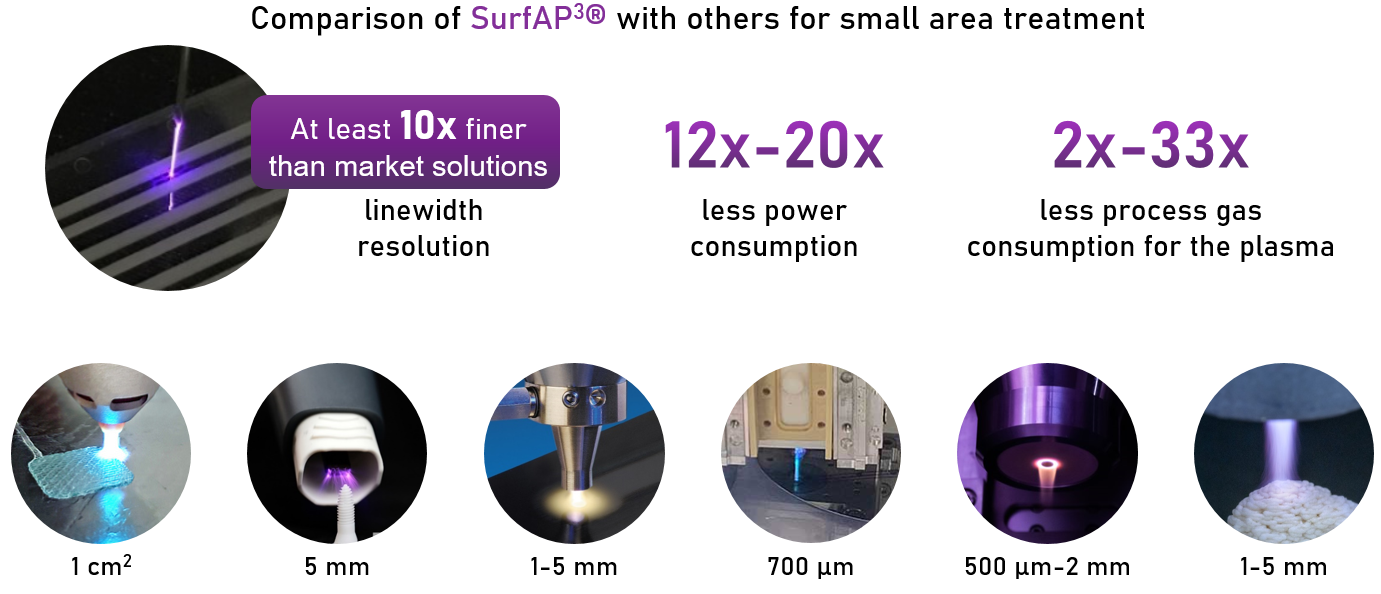